Bucket Elevator Explosion Protection
The combination of a bucket elevator’s large volumes, dusty materials and numerous moving parts creates the necessary conditions for a potentially explosive environment which requires effective mitigation solutions.
How Does It Work?
Test Protection On Your Bucket Elevator
This easy-to-use tool helps confirm which protection methods are available for your equipment based on its handled dust type, size, location and more. Results and recommendations are then emailed to you for your records.
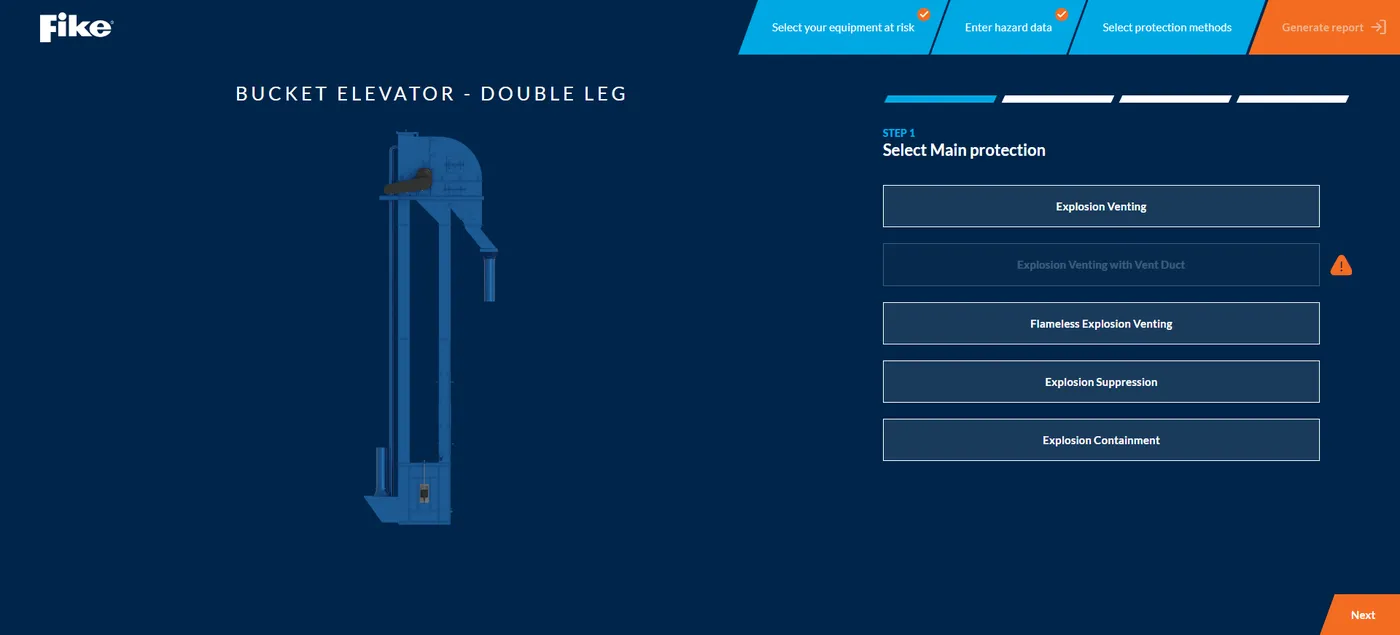
Dust Hazards And Ignition Risks
Bucket elevators suspend dust primarily in the boot and head sections, where product rapidly enters and exits the enclosure, respectively. The head and boot are the most likely segments to experience a deflagration due to their amount of open space containing dust clouds, the possibility of product accumulation which may smoulder or catch fire, and the multiple prospective ignition sources present in these areas, including:
- Internal equipment failure like buckets, fasteners or bolts coming loose.
- Friction causing a belt to become misaligned or slip off the pulley.
- Overheated pulley bearing.
- Metallic impurities in product flow.
- Ember from an upstream conveyor entering the bucket elevator.
Upon ignition in the head or boot, and without reliable protection, the deflagration will likely propagate through the legs, into inlets and outlets (leading to silos, or other processing equipment), and through de-dusting lines (typically leading to cyclones or dust collectors).
The construction and operation of bucket elevators is such that combustible dust clouds and potential ignition sources are omnipresent. Therefore, explosion protection is vital to protect workers, equipment and business continuity.
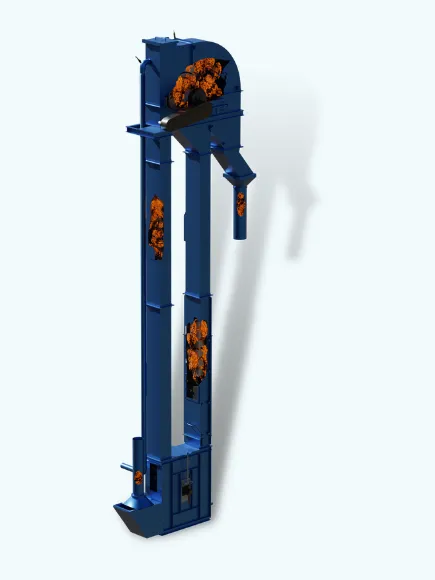
The Solutions
The likelihood of bucket elevator explosions can be largely reduced by:
- Bearing temperature monitoring.
- Belt alignment monitoring.
- Metal detectors.
- Spark detecting and extinguishing systems.
- Antistatic belt material.
- Lowering transport speed.
However, while these preventative methods are effective at reducing the frequency of explosions, they do not mitigate the destructive effects of explosions that do still occur.
The most widely accepted and recognized explosion mitigation options include explosion venting or suppression systems to protect the bucket elevator, coupled with isolation to prevent propagation into connected equipment such as a silo.

1. Protecting the Vessel: Explosion Venting
Explosion vent panels are one of the most economic and convenient solutions to prevent explosions from reaching their potential maximum pressures.
When a deflagration occurs, vent panels serve as the weak point of the enclosure and provide a pathway for expanding pressures and flames to escape. On bucket elevators, explosion vents are often installed on the head, boot and on both sides of the legs to create equal reaction forces.
Fike designs and manufactures explosion vent panels specifically for bucket elevators. EleGuard is a cost-effective, single-element explosion venting device venting device which can be easily installed weld-free without additional mounting frames by riveting just six bolts, and complies with all standards and installation requirements disclosed by NFPA. When flames must be extinguished in certain applications (such as indoor bucket elevators), Fike EleQuench flameless vents maybe installed over Fike EleGuard to make venting safe in these environments.
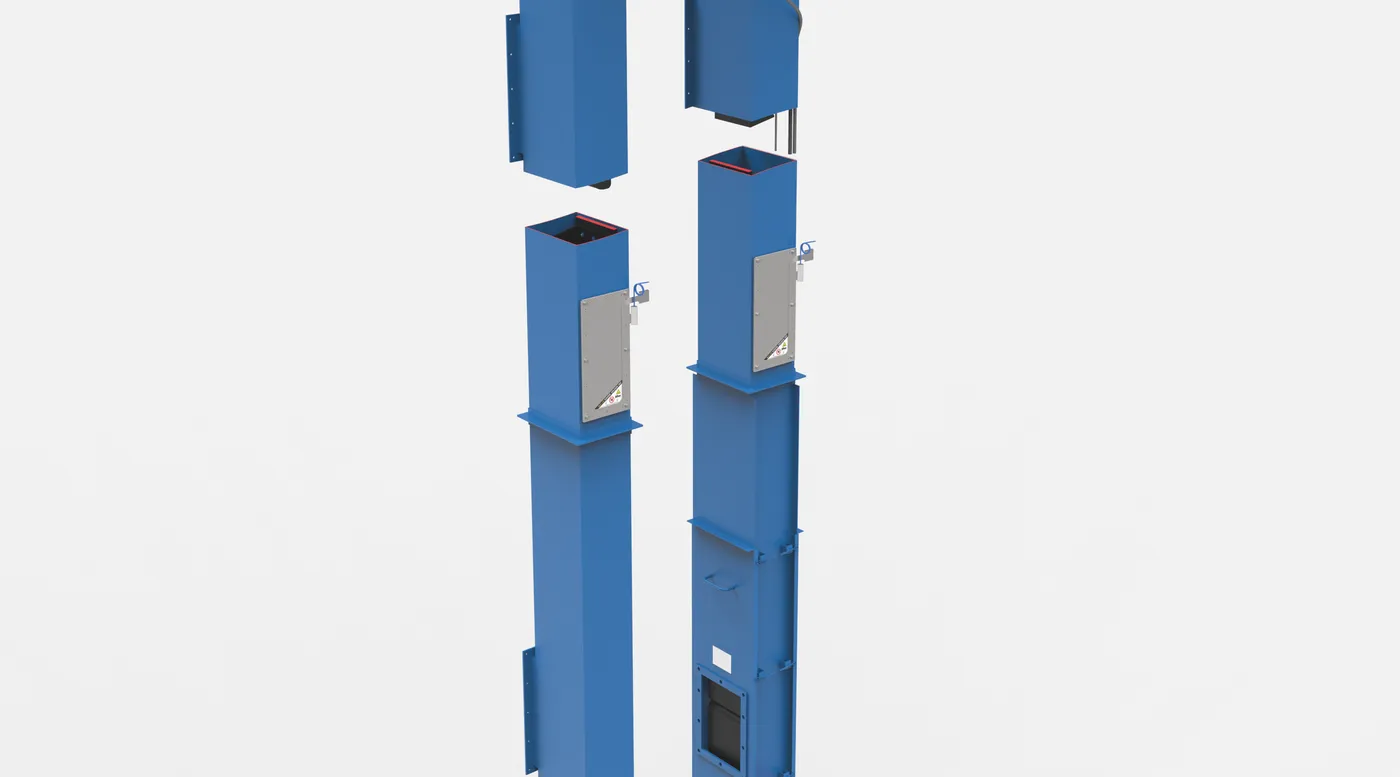
2. Protecting the Vessel: Explosion Suppression
Like venting and flameless venting, explosion suppression systems are also designed to mitigate the initial deflagration. When the incipient stages of a deflagration are detected by an active Fike detection and control system, the Fike HRD bottle fully releases its contents of sodium bicarbonate into the bucket elevator to suppress the deflagration - all within milliseconds of ignition.
Suppression systems may be recommended or required in favor of venting solutions for the following reasons:
- Reduces the pressure of deflagration to protect enclosure integrity.
- Extinguishes the flame within the bucket elevator, reducing fire damage potential.
- Eliminates the flame release and greatly reduces the pressure path associated with explosion venting.
- Can be used in combination with explosion venting for the indoor section of the elevator enclosure.
- Largely eliminates the discharge of toxic or hazardous materials outside of the elevator enclosure.
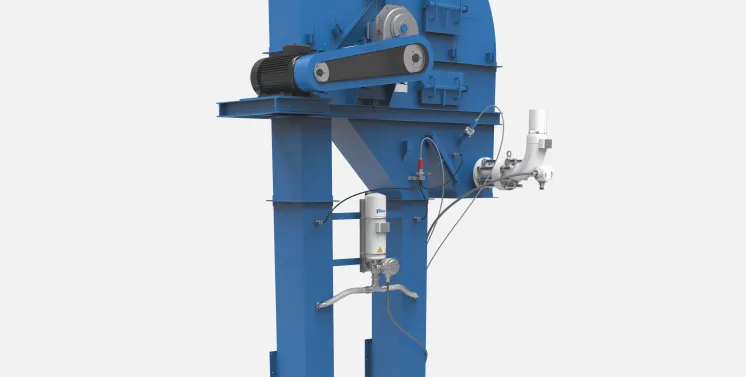
3. Protecting Connected Equipment: Isolation
Because bucket elevators are often connected to many other parts of the systems, explosions can spread into connecting pipes and processing equipment, potentially damaging the rest of the facility other than just the bucket elevator.
Therefore, to keep explosions contained to the vessel in which the deflagration originated, explosion isolation is required.
Traditional explosion suppression and isolation systems use pressure sensors to detect the pressure wave of an explosion; however this may not be adequate for the protection of bucket elevators. Testing has proven that the explosion will have already spread several meters into the leg section and into connected pipes, and will have become violent before detectable pressure is generated.
Therefore, the use of infra-red sensors to monitor optical radiation is often required. These sensors are installed around the boot and head sections, where ignition is likely to originate.
Chemical isolation bottles (Fike SRDs) are placed on the feed, discharge spouts or aspirating ducts to prevent flame from propagating upstream and downstream into connected pipes and vessels. SRDs provide rapid discharge of a chemical suppressant, which is impenetrable to flames.
Fike’s chemical isolation advantages include:
- Designed for easy maintenance.
- Variety of suppressant agents protects against a wide range of hazards.
- Easily recharged, minimizing downtime.
- Low pressure monitoring and continuous system integrity supervision.
Finally, certain bucket elevators may be protected entirely with passive mitigation strategies. In these scenarios specific designed explosion protection systems in the secondary vessel will be required.
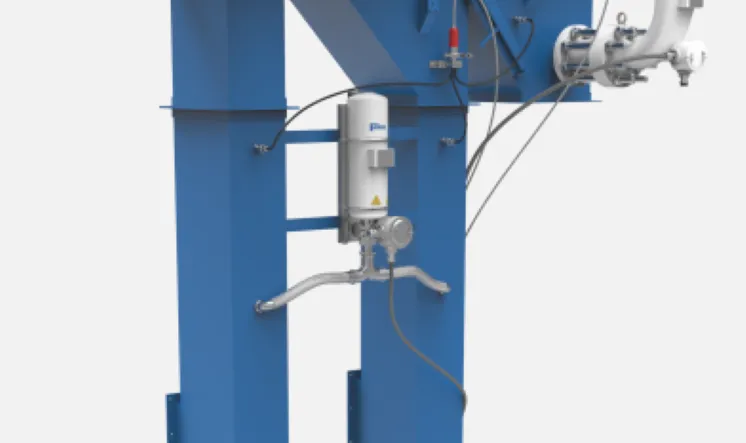