Explosion Protection For Cyclones
Cyclones may be protected with “passive” or “active” systems depending on several factors such as the location of the equipment, the aggressiveness of the dust, lower total cost of ownership, and more. Passive explosion protection systems react to a deflagration’s pressure, while active explosion protection includes electronic detection and control which activates connected systems within milliseconds of detection.
How Does It Work?
Test Explosion Protection On Your Cyclone
This easy-to-use tool helps confirm which protection methods are available for your equipment based on its handled dust type, size, location and more. Results and recommendations are then emailed to you for your records.
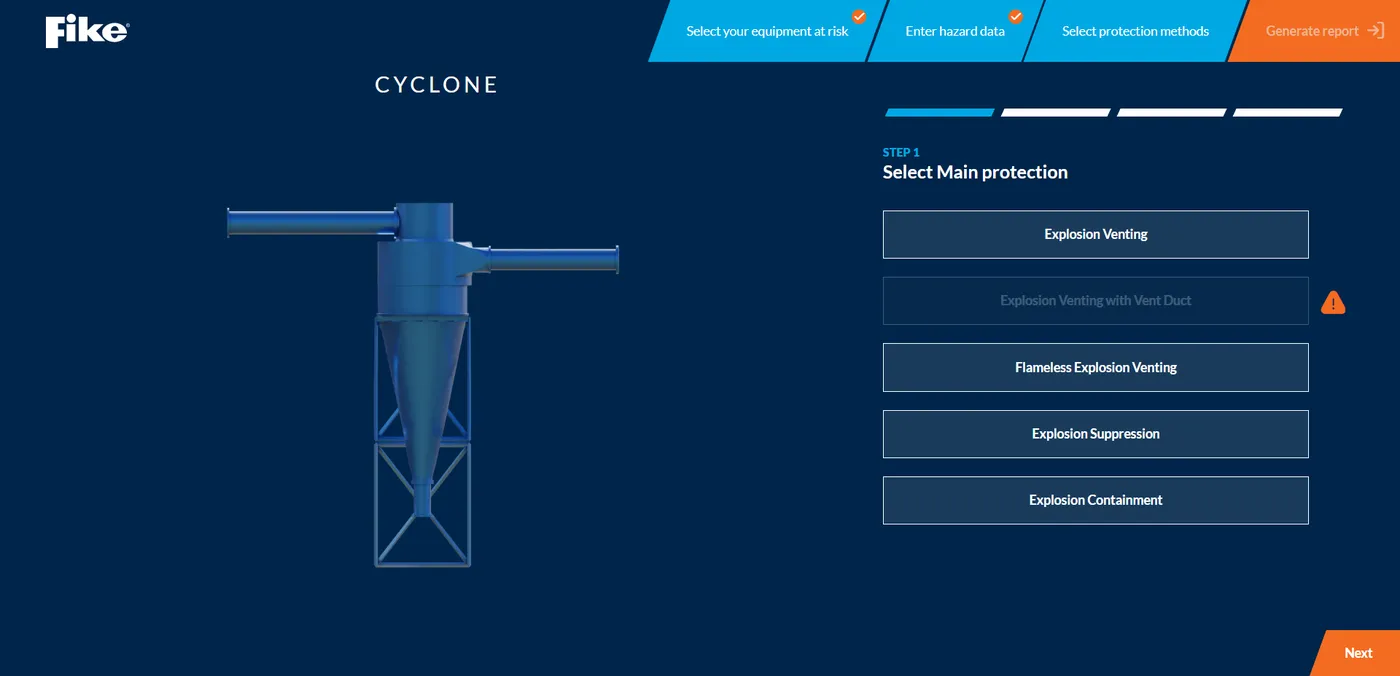
Dust Hazards And Ignition Risks
Unlike other processing equipment such as dryers, conveyors or mills, cyclones rarely consist of any moving parts; therefore, very few ignition sources exist within a cyclone.
This is why cyclones are rarely viewed as a “primary dust hazard,” or a vessel from which a deflagration will originate.
The more likely hazard, and concern, is for a deflagration to occur within a connected vessel. For example, a smouldering clump, a hot foreign object or an ember could ignite the outlet hopper of an upstream mill, which would then propagate downstream into the cyclone’s own combustible environment and create even more devastation.
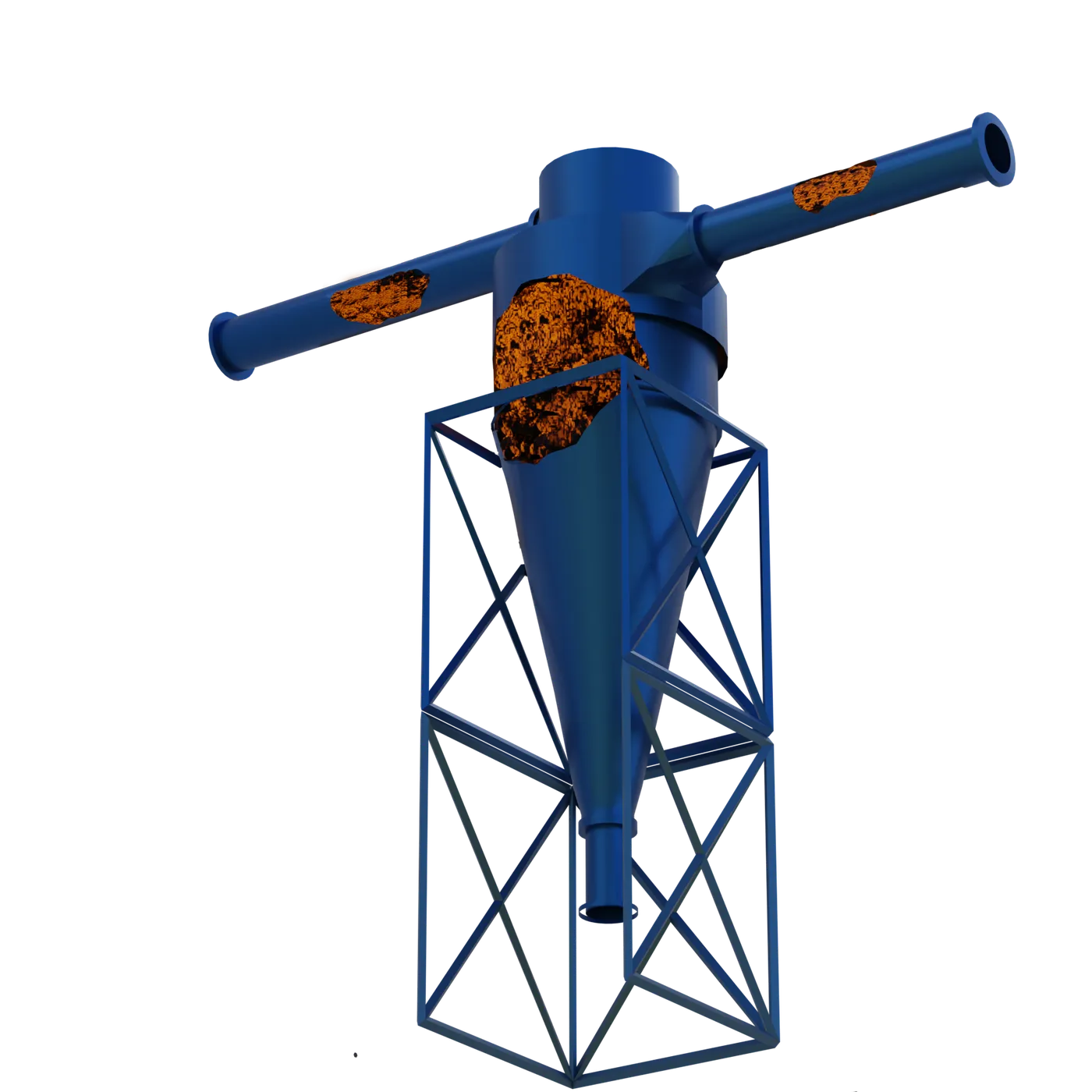
The Solutions
Due to cyclones’ fine dust particles, interconnectivity to other equipment of the process, and prevalence of dust accumulation and dust clouds, explosion prevention and good housekeeping efforts may be employed to reduce the ignition risk. These preventative measures may include:
- Regular cleaning of the cyclone and keeping connected ducts free of dust.
- Spark/ember detection and isolation or suppression on dirty air inlet.
- Temperature supervision on clean air outlet.
- Carbon monoxide monitoring on clean air outlet.
However, while prevention methods may effectively reduce ignition risks, it’s impossible to eliminate the chance of an explosion altogether. The outcome of a DHA or other risk assessment is often the requirement of an explosion mitigation and isolation systems are implemented to protect against the irreparable effects of a worst-case scenario.
1. Protecting the Vessel: Explosion Venting
Explosion vent panels are one of the most economic and convenient solutions to prevent explosions from reaching their potential maximum pressures. When a deflagration occurs, vent panels serve as the weak point of the enclosure and provide a pathway for expanding pressures and flames to escape.
Explosion vent panels may be used if the cyclone is located either outside or near an exterior building wall or roof, allowing for vent ducting outside. Furthermore, enough venting area must exist on top of the shoulder (for rectangle vents) and/or on top of the hat (for round vents). Vents are rarely installed on the cyclone’s sidewalls, as this may disturb the cyclonic effect.
For cyclones located indoors, not near walls that would allow for vent ducting, and with enough venting area, flameless venting may be installed. A flameless venting device is placed on top of the explosion vent panel. The flameless venting device contains a flame filter that extinguishes the explosion flames and additionally a fine particle retention screen which prevents unburnt fuel from being discharged, preventing secondary explosions outside the vessel.
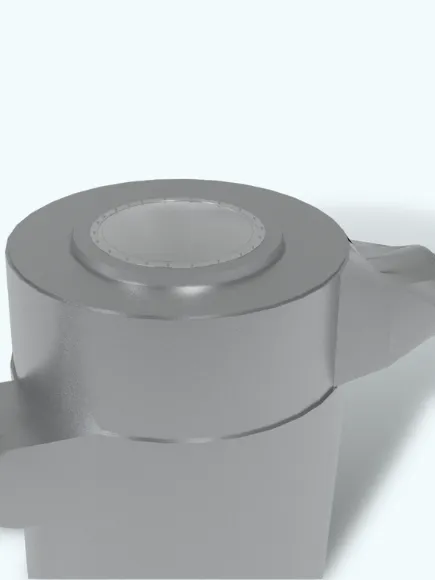
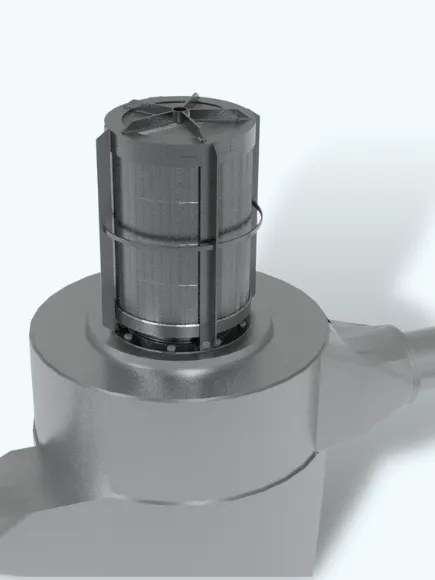
2. Protecting the Vessel: Explosion Suppression
Similar to explosion venting, explosion suppression systems are also designed to mitigate the initial deflagration. When the incipient stages of a deflagration are monitored by a pressure or optical detector, the explosion protection control system will activate the suppression container to fully release its contents of sodium bicarbonate into the cyclone to suppress the deflagration - all within milliseconds of ignition.
Suppression systems may be recommended or required in favor of venting solutions for the following reasons:
- Reduces the pressure of deflagration to protect enclosure integrity.
- Extinguishes the flame within the cyclone, reducing fire damage potential.
- Eliminates the flame release and greatly reduces the pressure path associated with explosion venting.
- Largely eliminates the discharge of toxic or hazardous materials outside of the cyclone.
HRD suppression bottles are primarily installed on the hopper, but when necessary, on the sidewall’s “armpit,” the area just before where the material enters the cyclone. This allows the material to make one rotation and begin to descend the cyclone, thus protecting the HRD nozzle from high-velocity materials.
HRDs are typically equipped with a telescopic spreader, which only protrudes into the vessel when called upon, to avoid dust buildup and disturbance of cyclonic operation.
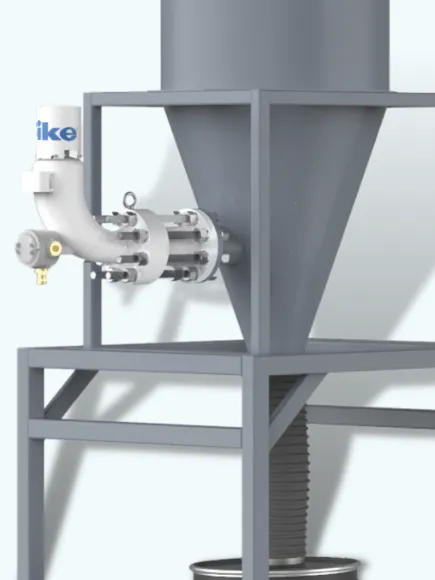
3. Protecting Connected Equipment: Isolation
Isolating the cyclone from connected equipment is a key component of a reliable explosion protection system. This may be achieved with either an active or passive isolation system.
If venting is used to protect the vessel, Fike’s Dual-Flap Isolation Valve (DFI™) is often used; if suppression is used to protect the vessel, chemical barriers are often chosen to isolate the dusty air inlet. An active mechanical barrier may be preferred to a chemical barrier if pressure wave propagation is of concern or when a DFI is not preferred due to the expected product abrasion.
Like the air inlet, if venting is used to protect the cyclone, passive isolation is often used to isolate the air outlet. Otherwise, active isolation is recommended because a detection and control system will have already been installed on the cyclone to support suppression.
Lastly, the collection bin/hopper may not require protection if the rotary valve between the discharge receiver and cyclone is third-party approved as an explosion isolation device and activates quickly enough upon explosion detection. If the rotary valve isn’t capable of explosion isolation, a chemical barrier or active mechanical isolation valve would be needed.
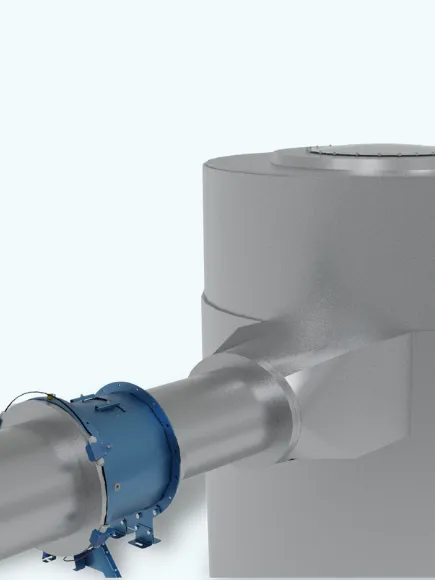
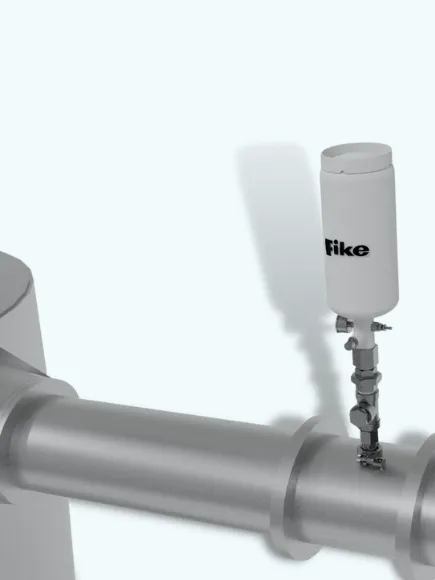
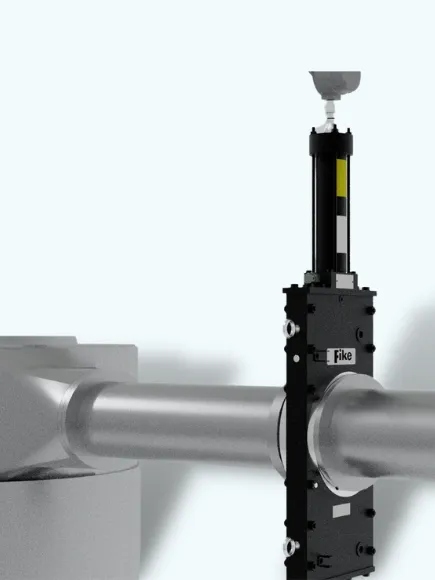