Explosion Isolation Systems
Explosion isolation systems prevent combustible dust explosions from propagating from one area of the production process to another, thereby eliminating the possibility of devastating secondary explosions from occuring.
How Does “Passive” Explosion Isolation Work?
How Does “Active” Explosion Isolation Work?
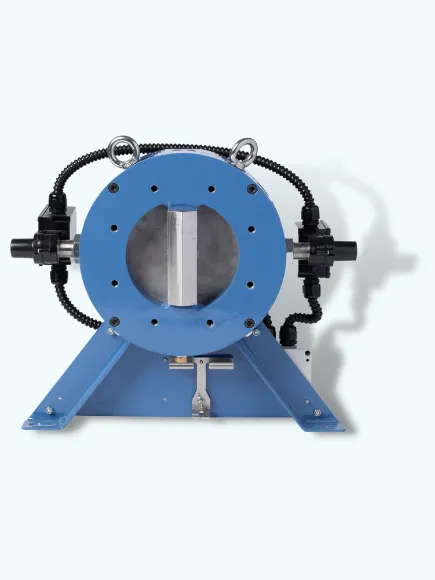
Dual-Flap Explosion Isolation Valve (DFI™)
A compact, lightweight dual-flap isolation valve held open by normal process flow until the pressure of a deflagration forces DFI to close rapidly into a locked position, preventing the explosion flame and pressure to propagate upstream into connected equipment.
Learn More1. Flexible Installation
Engineered to perform reliably in both horizontal and vertical pipes, and close to bends. May also be installed closer to a vessel than most other flap valves due to its fast-closing, lightweight flaps. Datasheet »
2. Wide Application Range
Protects against most dust hazards: common organic dusts, light metal dusts and low MIE dusts. Suitable for dust-laden inlet line of dust collectors and product receivers, or clean-air intake lines of dryers, mills and conveyance systems.
3. Stainless Steel Option
Protect against rust, paint or other contaminants from entering the product.
4. Tested in Real-World Applications
Many flap valves are certified for pressures for which they haven’t been accurately tested. DFI testing exceeds EN16447’s standards by including a protected zone pipeline, holding flaps in an open position until the precise time of ignition or flow reversal, and using explosion vent panels instead of open venting ports. Read more »
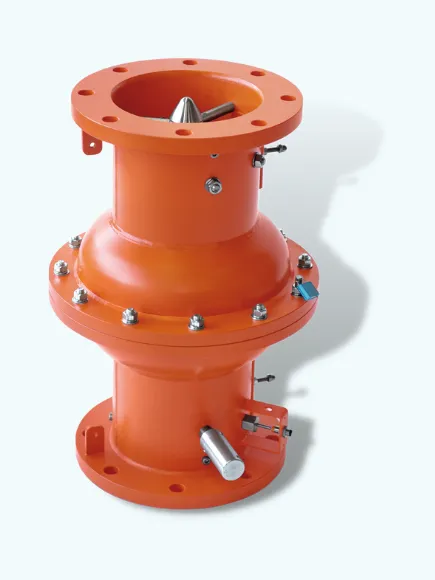
Bi-Directional Explosion Isolation Float Valve (VENTEX™)
Equipped with a spring-loaded poppet, which during a deflagration is pushed against the spring by the pressure wave into a mechanically locked position.
Datasheet1. Bi-Directional
Isolates explosions propagating with or against the process flow.
2. Wide Application Range
Suitable for clean air intake and outlet lines of cyclonic separators, dust collectors, dryers, mills and conveyance systems, and protects against gas, hybrid or dust hazards including organic and metal dust.
3. High Compatibility
Used in vented, suppressed and contained vessels up to 12 barg, and available in stainless steel and gas-tight configurations.
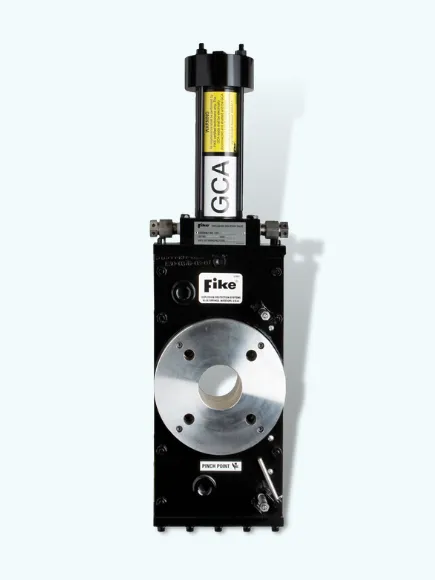
Active Explosion Isolation Gate Valve (EIV)
Mechanical barrier which prevents the spread of flames and pressure by closing within milliseconds of detection, effectively preventing the deflagration from propagating through process piping or duct work. Available for duct sizes up to DN400.
Datasheet1. Bi-Directional
Isolates explosions propagating with or against the process flow.
2. Flexible Installation
Various mounting orientations, suitable for horizontal and vertical pipes and ducts.
3. Immune To Abrasive Dust
Suitable for organic and metal dust hazards, including aluminum deflagrations; and suitable for abrasive conveying applications, which may damage other types of isolation valves.
4. Hygienic Capabilities
Available with hygienic gate seal for low product buildup, and available in pharmaceutical execution with capability of full cleanabilty inside and outside; wetted parts do not contaminate food product.

Explosion Isolation Pinch Valve (EIPV)
Utilizes a rugged elastomer sleeve and compressed air to pinch the device to full closure within milliseconds, protecting downstream equipment from flames and pressure. Available for duct sizes up to DN150.
Datasheet1. Bi-Directional
Isolates explosions propagating with or against the process flow.
2. Prevent Explosions
Can be used to prevent sparks from entering into processing equipment in conjunction with its main explosion isolation function.
3. Quick Reset
Can be easily reset after activation by user; no refurbishment needed.
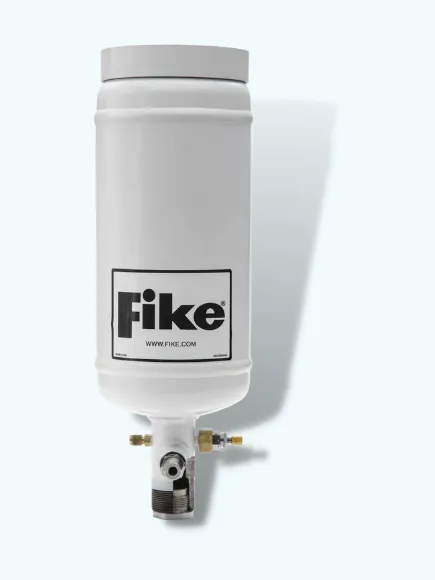
Chemical Explosion Isolation (SRD)
Rapidly discharges suppressant agent and inert gas into ducts, pipes and conveyors to create a heat-absorbing chemical barrier which isolates flame propagation into connected vessels.
Datasheet1. Flexible Installation
May be applied on small and large, round and rectangular ductwork or conveyors, and with short installation distances from the hazard due to its fast-acting delivery.
2. Mechanical Conveyance
Can be applied on mechanical conveying ducts, such as screw, belt or chain conveyors and bucket elevators.
3. Flexible Mounting
Flexible mounting orientations available to ensure efficient delivery of agent into the application.
4. Quick Reset
Field rechargeable which assures fast reset and low downtime after explosion.
Fike Isolation System Design
Each Explosion Isolation System is custom designed specifically to mitigate your hazard risk and meet the needs of your application and business. This is based on your unique combination of hazard, equipment to be protected, interconnections, location, regulatory and operating conditions.
As part of this design process Fike prepares a full system design where the following parameters are calculated by qualified Fike personnel:
- Detector and isolator type, quantity and installation location.
- System operating and activation settings.
- Total reduced pressure.
This data can be used to:
- Guide your mechanical installation team or contractor.
- Evaluate your equipment’s capability to withstand the recoil forces that may arise during an explosion event.
The final system design document can be added to your explosion hazard and protection files to be submitted in case of a safety inspection.
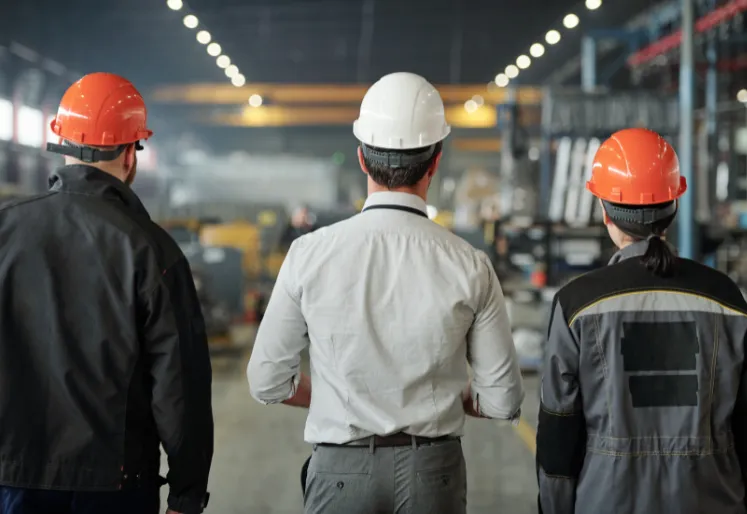
Test Explosion Isolation On Your Equipment
This easy-to-use tool helps confirm the safest and most cost-effective protection methods for your equipment based on its handled dust type, size, location and more. Results and recommendations are then emailed to you for your records.
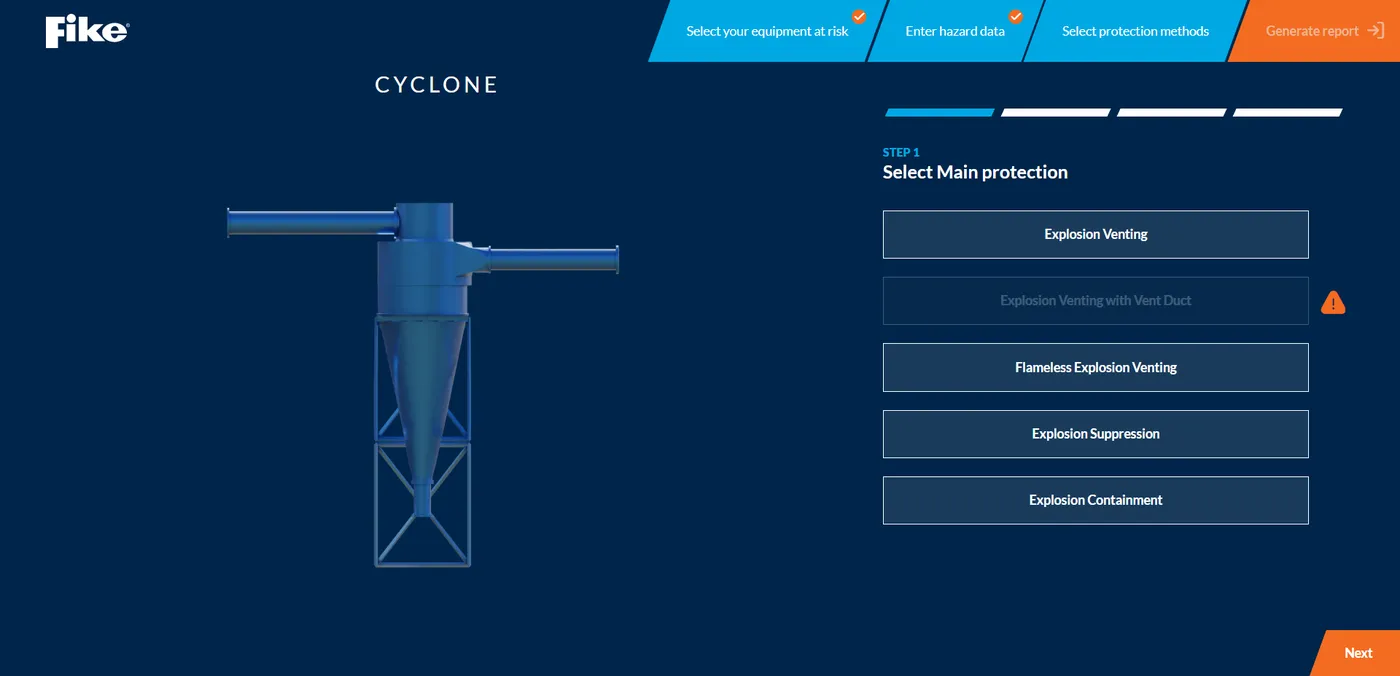
Once your protection systems have been selected, you may rely on Fike’s global field technicians to perform:
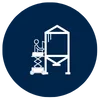
Installation
that precisely replicates system design drawings and is performed during a convenient time in your production schedule. Full turnkey installation is also available when required.
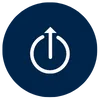
Commissioning
of active explosion protection systems to ensure that electrical, PLC and other connected processes work as intended.
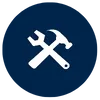
Maintenance
which may include quarterly inspections to maintain compliance or emergency maintenance when you need us most. Flexible service level agreements provide guaranteed response times according to your business needs.
What are the benefits of passive explosion isolation?
During normal operation, passive isolation devices are held open by process flow or a spring retention device and are closed from the pressure wave of a deflagration; therefore, no explosion detection and control system is required for activation.
- Often the more cost-effective explosion isolation solution.
- Requires no electronic detection systems.
- Installation doesn’t typically require specially trained personnel.
- Maintenance requirements are minimal and easy to perform significantly reducing downtime.
- May be combined with active isolation systems.
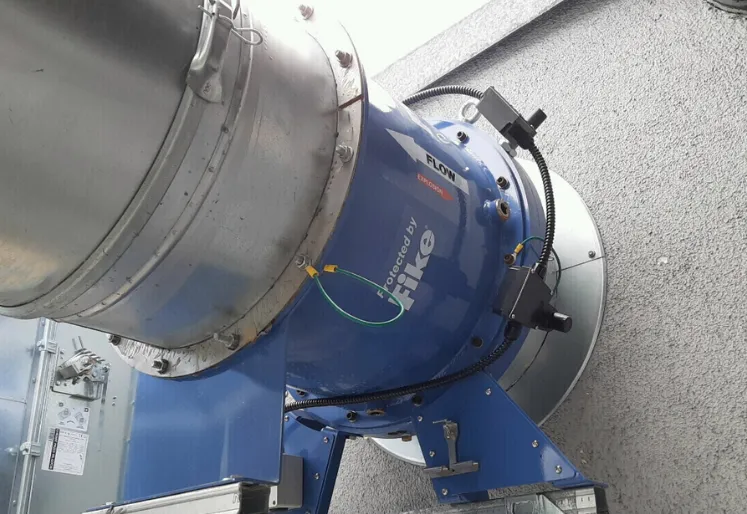
What are the benefits of active explosion isolation?
During the very early stages of combustion, a pressure or optical detector will detect the impending deflagration and send a signal to the EPACO™ system, which will then activate necessary suppression or isolation valves at the onset of the explosion.
- Minimal equipment damage when combined with explosion suppression, fast reset and fast resumption of production process.
- State-of-the-art detection algorithms result in the highest possible level of reliability for precise activation and to eliminate risk of nuisance activations.
- Unintrusive to the process and does not cause product buildup and pressure drop.
- Electronic supervision of system status and trouble indication allows for full system diagnostics for protection system optimization, event history and post-activation analysis.
- May integrate into process control and visualization systems.
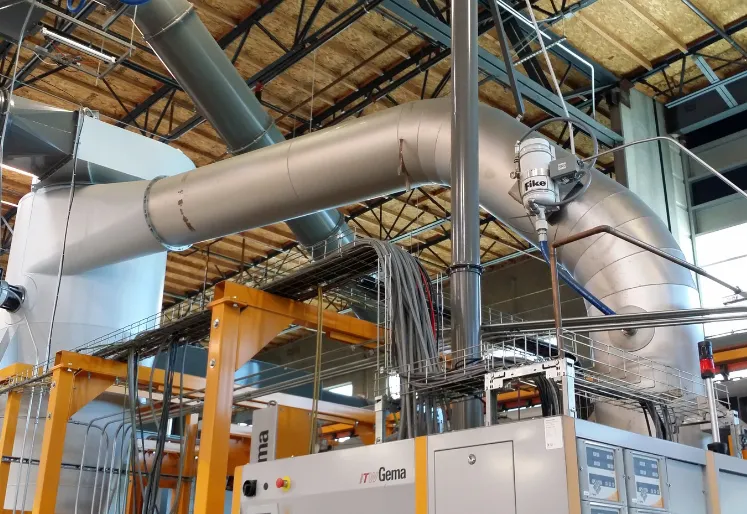
When is active explosion isolation recommended?
Various types of dust hazards and geometries of processing equipment may not be reliably protected with passive explosion protection systems, which have some inherent limitations. Active explosion isolation systems may be recommended in the following situations:
- Post-explosion fire risk must be reduced by not allowing the ingress of oxygen after an explosive event.
- Minimal interaction with conveyance flow through duct is required.
- Many types of conveyors such as screw, belt or chain conveyors, and other volumes such as elevator legs can often only be isolated with chemical barriers.
- Downtime after an explosion event must be as minimal as possible.
- When suppression is used to protect the main volume, chemical isolation may be the most cost-effective isolation method because a detection and control system will already be required.
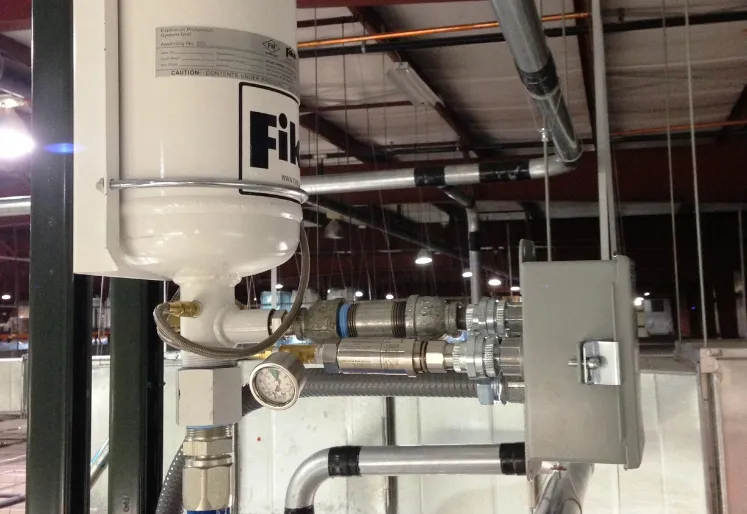