Explosion Protection Systems
Fike is one of the world’s most trusted manufacturers of reliable explosion protection technologies for nearly any industry and application. You can be sure that when a Fike product is called upon, it works precisely as intended.
Test Explosion Protection On Your Equipment
This easy-to-use tool helps confirm which protection methods are available for your equipment based on its handled dust type, size, location and more. Results and recommendations are then emailed to you for your records.
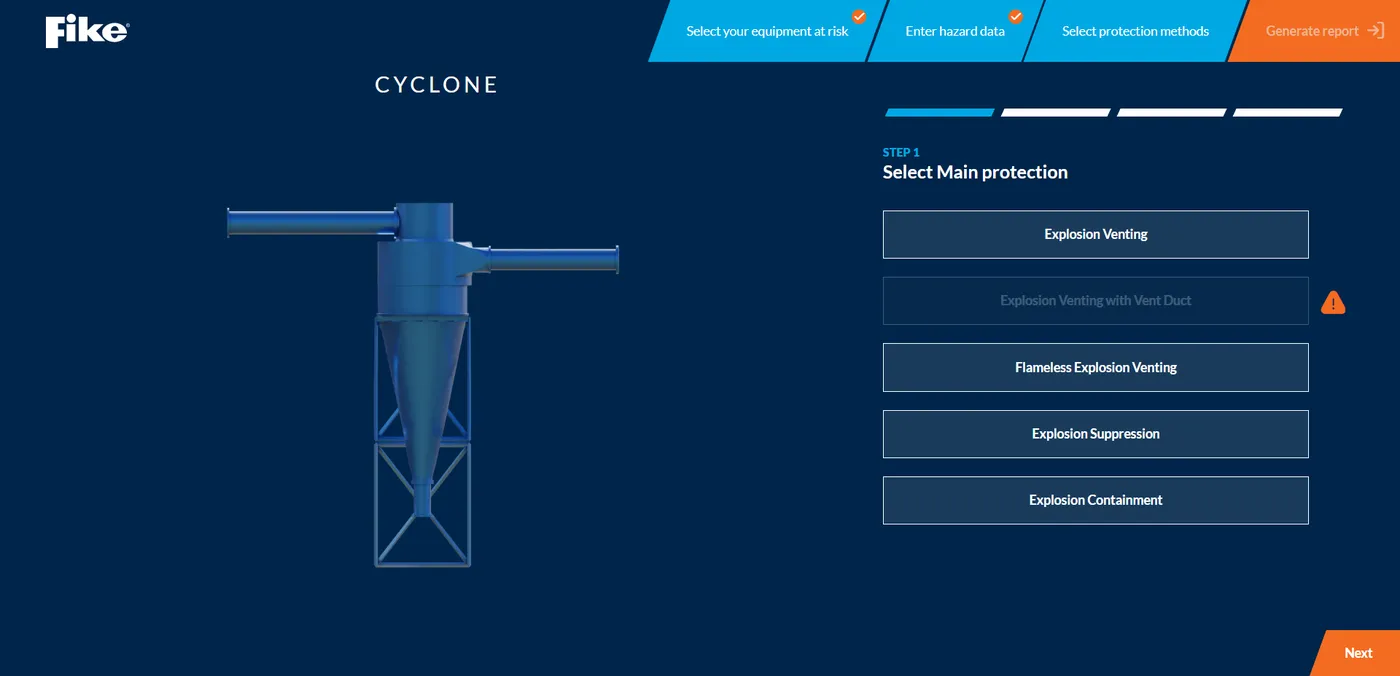
Fike explosion protection systems are supported by our:

System Design Team
Determines hardware type, size, quantity and position to meet your protection objectives and minimize effects on your daily operation.

Global Field Service Team
May help with installation, commissioning and maintenance of your explosion protection system to confirm compliance with standards and the safety of employees.

Testing & Innovation Center
Ensures Fike products meet applicable testing standards and are validated to perform under real-world conditions they may experience during an actual deflagration.
Explosion Detection & Control
Less than 2 ms electronic delay between presence of explosion pressure and activation of suppression and isolation devices ensures low Total Suppressed Pressures, closer installation of isolation devices to the protected volume and a reduced total cost of ownership.
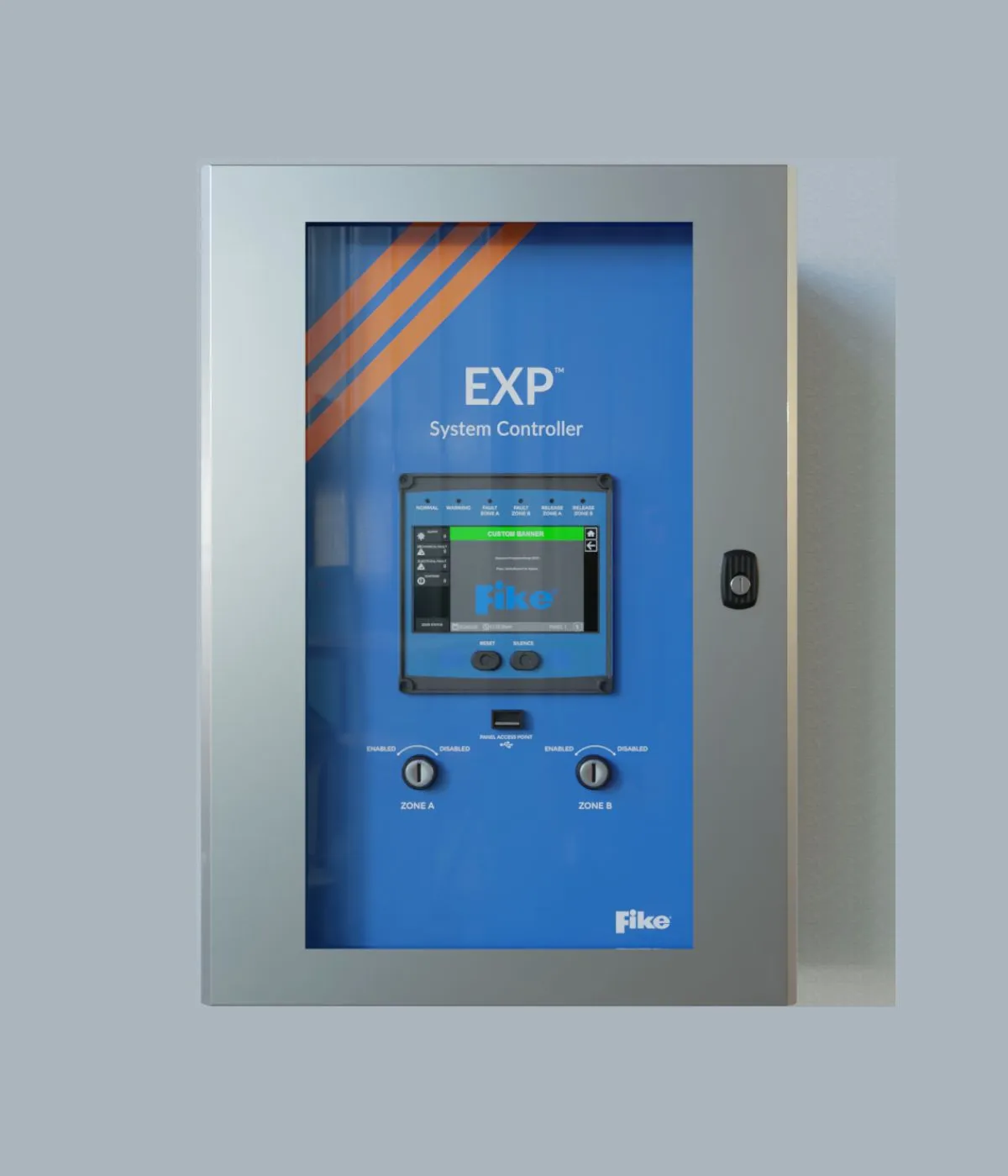
Explosion Controller
EXP®
Function
Explosion protection control system for use with Fike detection, suppression and isolation devices.
Benefit
- Interactive touch screen display relays easy-to-interpret system information
- Simple navigation allows you to monitor the status of all connected devices
- Future proof your explosion protection system for any new or cross-functional technologies developed by Fike
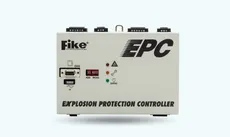
Control
EPACO®
Function
Explosion protection control system for use with Fike detection, suppression and isolation devices.
Benefit
- Modular system allowing cost-effective sizing and expansion
- Status and safety function supervision of the entire protection system
- Tailored detection algorithms for the highest possible system stability and reliability
Approvals
- NFPA69 compliant
- FM5700 approved
- ATEX EN14373 & EN15089 certified
- SIL2 IEC61508 certified
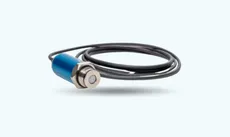
Pressure Detection
Ceramic, Stainless Steel
Function
Detects pressure rise in the early stages of an explosion.
Benefit
- Multiple mounting styles and the possibility to configure multiple detectors and functions increase system stability
- Multiple detector variants for extreme temperature, vibration, hygienic applications and sticky or course solids
Approvals
- NFPA69 compliant
- FM5700 approved
- ATEX EN14373 & EN15089 certified
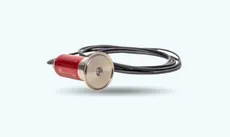
Optical Detection
IR Optical Detector
Function
Detects infrared light radiated by the incipient explosion.
Benefit
- Multiple mounting styles increase system stability
- Multiple detector variants for extreme temperature, vibration, hygienic applications and sticky or course solids
- Fiber optics for multi-spot detection
Approvals
- NFPA69 compliant
- ATEX EN15089 certified
Spark Detection & Suppression
Installed on the processes’ conveying lines, a Fike Spark Detection and Suppression System uses optical detectors to quickly detect even the smallest amounts of infrared radiation. Upon detection, a small amount of extinguishing water mist is injected into the conveying line to extinguish the spark, the process control system is signaled to shut down the process, and the source of the sparks may be rectified before resuming production.
- Includes various detector options (spark, ember, dual-spark ember), spark detection and suppression system controller, water injection nozzle(s), and water storage and/or feed system.
- May be used on a wide range of applications, including on conveying lines of dust collectors, cyclones, mills or anywhere else sparks may be generated and conveyed into a dust cloud.
- VdS and ATEX approved, and are currently in use in more than 30,000 field installations around the world.
- Multiple control unit sizes to protect up to 36 conveyance lines, and wide selection of pressure boosters, pumps and water storage system.
- Note: Spark suppression systems use water as an extinguishing agent, which may not be acceptable in certain processes. Alternative protection methods such as pinch valves or gate valves may be used to isolate the spark rather than extinguishing it with water.
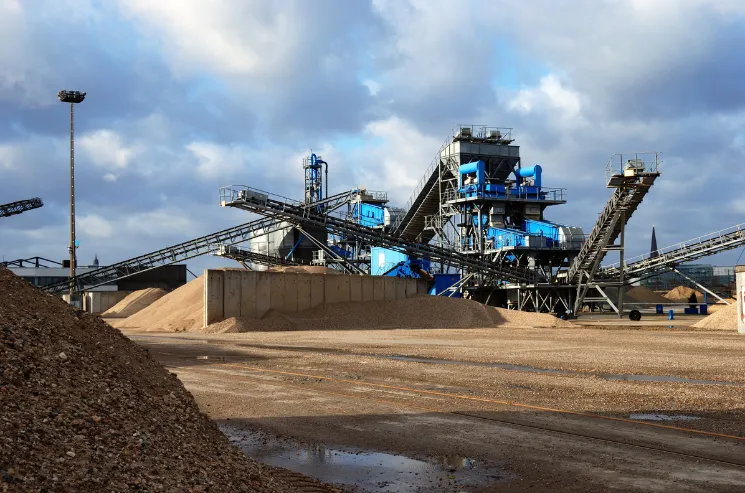