Explosion Venting
Often the most cost-effective explosion protection methods, explosion vent panels relieve a deflagration’s pressure and flames from the vessel in order to keep its total pressure below its design pressure.
How Does Explosion Venting Work?
How Does Flameless Venting Work?
When can flameless explosion venting be used?
Explosion venting may be used as a reliable explosion protection method when the vessel is:
- Located outside.
- Located inside but near an external wall to direct the pressure and flames outside.
- Equipped with enough surface area to support the required number of vents.
- Handling materials which are safe to release into the atmosphere.
When flames cannot be vented to a safe location, flameless explosion vents can often be installed on top of deflagration vent panels. These flameless devices allow pressure to escape the vessel and the flames to be extinguished by the flame filter, preventing secondary explosions.

Fike Venting System Design
Each Fike explosion venting system is custom designed specifically to mitigate your hazard risk and meet the needs of your application and business. This process is based on your unique combination of hazard type, equipment and its location, interconnections, operating conditions and regulations. As part of this design process, Fike prepares a full system design where the following venting parameters are calculated by qualified personnel:
- Size, burst pressure, quantity and type of vent panels and flameless venting devices, if applicable.
- Installation location within your equipment.
- External flame and pressure effects.
- Recoil forces on the processing equipment.
This data can then be used to:
- Verify whether there is enough space available on your equipment to install the vent panels.
- Verify whether there is sufficient space around your equipment to implement a safety zone (for the safe venting of flame and/or pressure).
- Guide your mechanical installation team or contractor.
- Evaluate your equipment’s capability of the recoil forces that may arise during an explosion event.
The final system design document can be added to your explosion hazard and protection files to be submitted in case of a safety inspection.
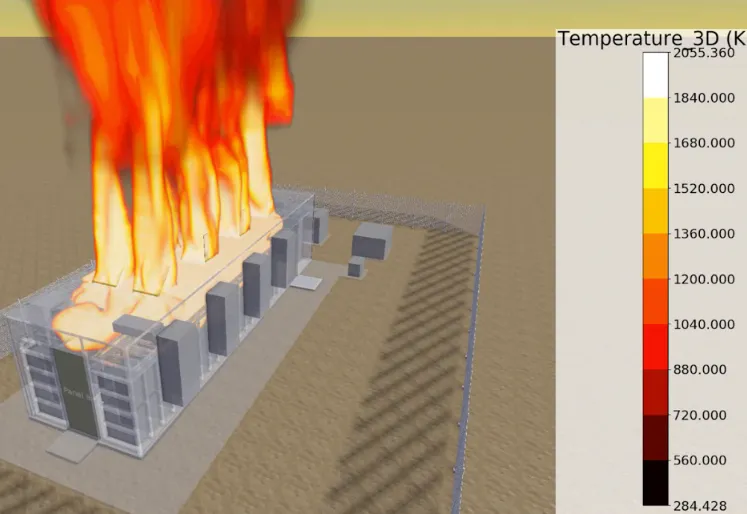
Explosion Vent Panels
Opens when the internal deflagration pressure exceeds the static burst pressure of the vent panel. The quantity of explosion vent panels, size and burst pressure are calculated based on the equipment volume, strength, and the fuel characteristics.
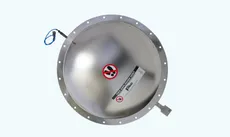
Standard Vents
Function
General purpose explosion vents for atmospheric, high temperature, vacuum and cyclic pressure applications.
Benefit
Many sizes and geometries available, that fit almost all applications.
Approvals
NFPA68 compliant
ATEX EN14797 certified upon request
Datasheets
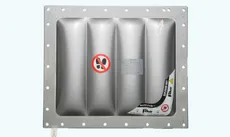
Hygienic
Function
Designed to protect hygienic atmospheric, elevated temperature and vacuum applications requiring minimal product agglomeration and washdown capability.
Benefit
Low installation cost due to:
- High venting efficiency
- Integrated top frame
- Overtorque protection
Approvals
NFPA68 compliant
ATEX EN14797 certified
Datasheets
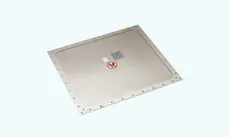
Hygienic+
Function
Designed for atmospheric and elevated temperature food and pharmaceutical applications requiring EHEDG-certified bacteria-free washdown capable vent panels.
Benefit
Low installation cost due to:
- High venting efficiency
- Integrated top frame
- Overtorque protection
Approvals
NFPA68 compliant
ATEX EN14797 certified
3A/EHEDG certified
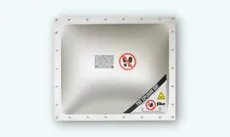
Battery Energy Storage
Function
Designed for atmospheric and elevated temperature food and pharmaceutical applications requiring EHEDG-certified bacteria-free washdown capable vent panels.
Benefit
Off gas analysis and large-scale testing used for economical application-specific venting solutions.
Approvals
ATEX EN14797
Datasheets
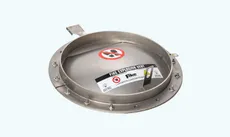
Gas Engine Exhaust
Function
Designed to protect against explosions in exhaust system of gas-fuelled engines.
Benefit
Unequalled, leak-free service life in high temperature, cyclic pressure and vibrations existing in gas engine exhaust piping.
Approvals
NFPA68 compliant
ATEX EN14797 certified
Datasheets
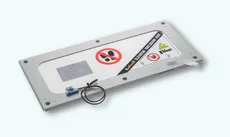
Bucket Elevator
Function
Designed to protect against dust explosions in bucket elevator.
Benefit
Low installation cost due to:
- Vent sizes that fit elevator legs
- High venting efficiency
- Weld-free, riveted installation
- Integrated top-frame
- Overtorque protection
Approvals
NFPA68 compliant
ATEX EN14797 certified upon request
Datasheets
Flameless Explosion Vent Devices
Placed over an explosion vent panel and contains a flame filter to extinguish the explosion flames while the explosion pressure is discharged into atmosphere.
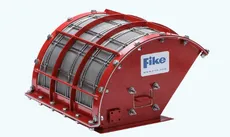
Standard
Function
General purpose flameless venting device for fine, coarse, fibrous and melting organic dust applications.
Benefit
Low impact on factory planning:
- Very small safety distance
- No external hazardous zoning required
- Not restricted by existing hazardous zoning
Approvals
NFPA 68 compliant
ATEX EN16009 certified upon request
Datasheets
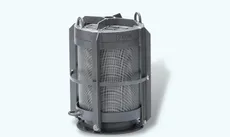
Performance
Function
Suited for metal dust applications and for corrosive or food production environments, due to full stainless steel execution.
Benefit
Low impact on factory planning:
- Very small safety distance
- No external hazardous zoning required
- Not restricted by existing hazardous zoning
Approvals
NFPA 68 compliant
FM Approved
ATEX certified upon request
Datasheet
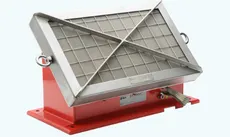
Bucket Elevator
Function
Designed to protect against dust explosions in bucket elevators.
Benefit
Low installation cost due to:
- Compact design with sizes that fit elevator legs
- High venting efficiency
Approvals
NFPA 68 compliant
ATEX certified upon request
Datasheet
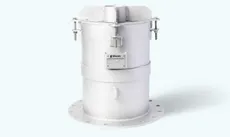
Gas Engine Exhaust
Function
Designed to protect against explosions in exhaust system of gas-fuelled engines, especially in manned areas or marine applications.
Benefit
Unequalled, leak-free service life in high temperature, cyclic pressure and vibrations existing in gas engine exhaust piping.
Approvals
NFPA 68 compliant
Datasheet
Test Venting On Your Equipment
This easy-to-use tool helps confirm which protection methods are available for your equipment based on its handled dust type, size, location and more. Results and recommendations are then emailed to you for your records.
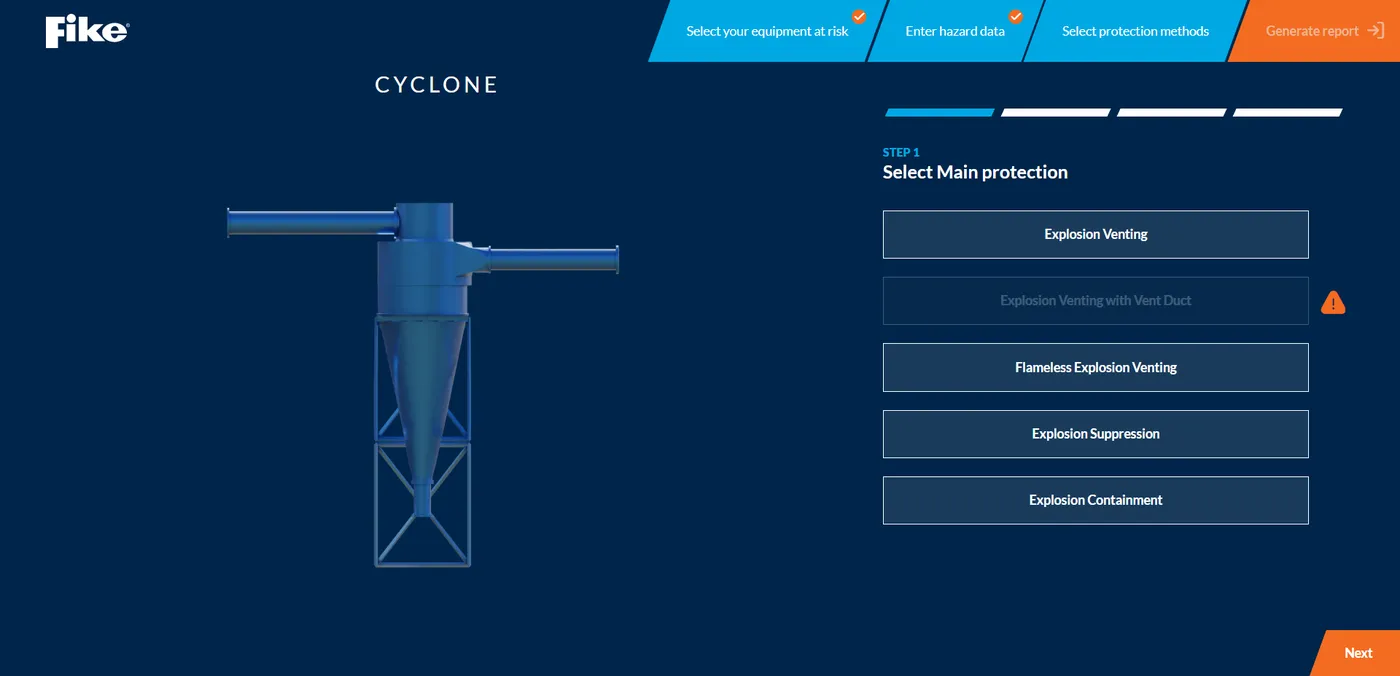
What are the advantages of explosion venting?
Explosion venting is a form of “passive” explosion protection, which means the device activates from the deflagration pressure itself. This results in the most cost-effective explosion protection solution due to its unreliance on an electronic detection and control system.
Furthermore, explosion venting can be applied on various sizes of industrial equipment with relatively hastle-free installation and minimal maintenance.
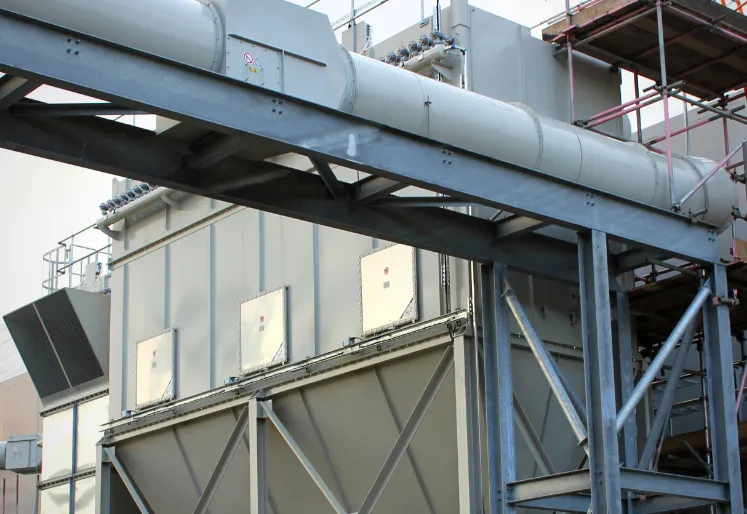
Are there any disadvantages of explosion venting?
While explosion venting is a cost-effective explosion protection solution, there are certain considerations before it can be used as a mitigation strategy.
Explosion venting does not prevent or extinguish an explosion. The resulting fireball can be up to 75 times the volume of the enclosure itself; therefore, the venting path must be directed toward a safe, untrafficked area. This may also result in post-explosion fires, so fire suppression systems are often required. Before resuming production, any damage to the process must be repaired and the vent panel must be replaced.
To avoid these disadvantages, explosion suppression is often used as an alternative to explosion venting.
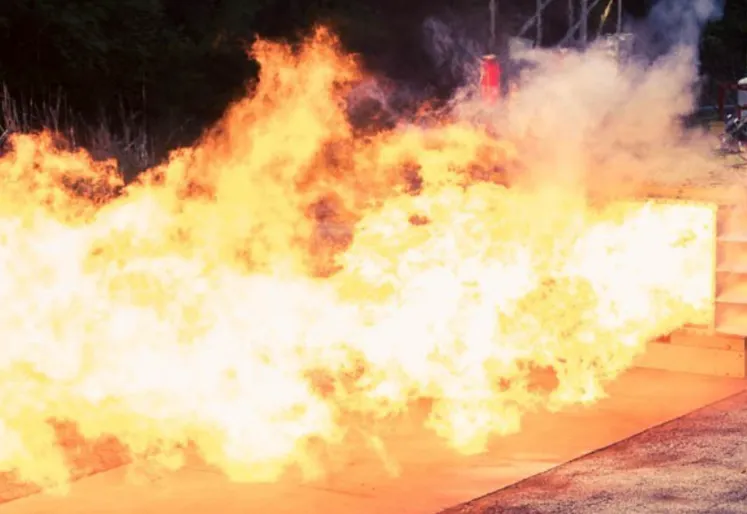
What are the differences between explosion vents and explosion doors/relief valves?
Explosion doors are heavier than vents and often require more venting area. If an explosion occurs, they do tend to fragment with dust of higher Kst values (dust explosion severity). Their opening pressure typically rises over time, due to corrosion and dirt, so they require regular maintenance. Finally, reclosing doors and valves may lead to a vessel implosion when combustion gases cool after the explosion.
However, one advantage of reclosing doors and valves is they prevent fresh oxygen ingress that could sustain the post explosion fire.
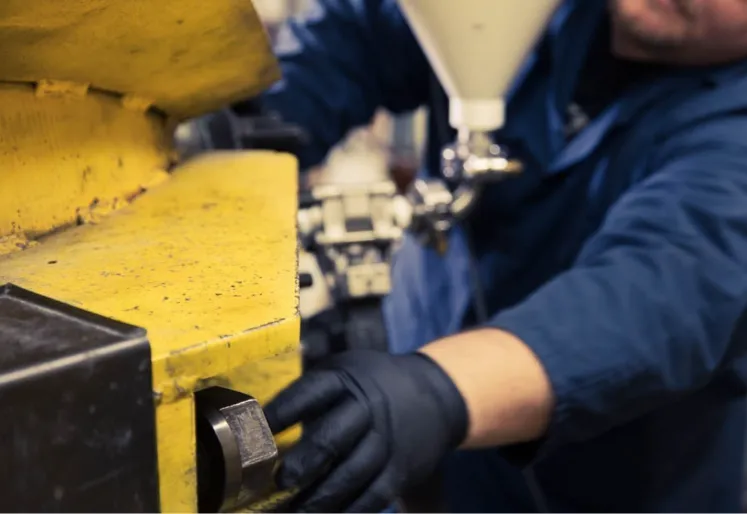
Who can design explosion vents for my unique process?
Fike’s applications team provides explosion vent design solutions for nearly any application. In addition to determining whether explosion venting is a viable protection strategy for your unique industrial process, our team of vent design experts will also calculate:
- Vent panel size, burst pressure, quantity and type.
- Installation location of panels.
- External flame and pressure effects.
- Recoil forces.
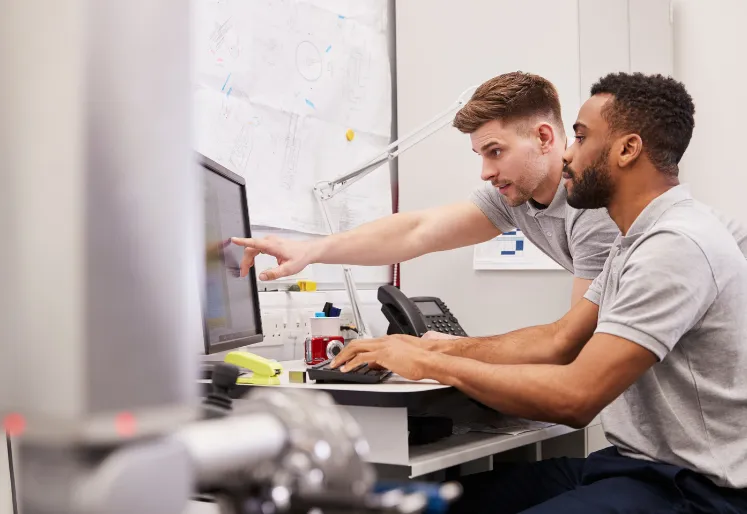