Cost, safety and legislation are the main drivers that are forcing chemical industry operators to come up with better products as well as better ways to prevent leakage that was previously tolerated and viewed as inevitable.
Nowadays companies can face huge fines based on unacceptable emissions of a leaked product. The product loss itself is already expensive and in addition there is the huge safety aspect of leaked hydrocarbons or toxic media. However, cost-effective ways to eliminate leakage from valves are available.
The chemical industry is one of the world’s largest with its sales exceeding $3 trillion in 2018. Due to its size and global activity the chemical sector has a big role to play in tackling climate change and achieving emission targets. Chemical products have a two-fold effect on greenhouse emissions (greenhouse gas or GHG’s): GHG’s are emitted during the manufacturing process whilst the use of many of these products may create a reduction of emissions.

“Preventing GHG’s from escaping to the atmosphere is a better approach than trying to reduce the effects of actually emitted products. One of the known emission sources throughout the processing industry are pipe and process equipment connections.”
Roger Bours
Currently the following types of chemical production have been identified as key areas where GHG’s emission reductions are prioritized: Ammonia production, urea production, ethylene production, chloralkali production, and bio-isoprene production.
With the chemical industries in Germany (28.4%), France (15%), The Netherlands (9.6%), and Italy (9.6%) being the most important, it would make sense for these industry leaders to further focus on emission reduction. Germany has so far been the only country where mandatory legislation is in place related to quantification of industry leakage.
Emission Control
The German “Technical Instructions on Air Quality Control” – also known as “Ta-Luft Regulations” – supported with industry standards such as VDI 2440 and DIN EN ISO 15848-1 have created an initial momentum in the reduction of actual fugitive emissions as the industry suppliers and users have been able to quantify the emission reductions.
The effect of this momentum is so far largely restricted to the German geographical area, with some smaller impact in the adjacent Austrian and Swiss regions and industries. Other European regions have little to no industry standards in place to assist in quantifying emission rates.
Preventing GHG’s from escaping to the atmosphere is a better approach than trying to reduce the effects of actually emitted products. One of the known emission sources throughout the processing industry are pipe and process equipment connections.
One commonly used type of industry connection is made through the use of flanges and gaskets. These seemingly “simple” connections are however sensitive to proper design, selection of gasket materials and bolting, installation and general wear and tear of the installation.
Part of the recognized industrial emissions occur through unanticipated or spurious leaks in process systems, e.g. leaking valves, pumps or flange connections. These “fugitive emissions” not only have an impact on the environment but also cause financial burden due to loss of potentially valuable materials and resulting plant inefficiency.
Through the use of specified Ta-Luft classified piping components the requirements for LDAR (Leak Detection and Repair) can be dramatically reduced, helping to lower the cost of ownership of the plant. Furthermore, the actual and ongoing quantification of total plant leakage can be determined and predicted over an extended period of operations.
An already proven method to achieve an immediate reduction of fugitive emissions is to prevent continuous leakages of process media which is happening through the use of critical safety devices such as pressure or safety relief valves. These devices are – by principle – continuously exposed to pressurized process media, whereas most pressure relief valves are prone to leakage.
The Fike ValveGuard concept offers the option of installing a Ta-Luft certified Rupture Disc device upstream of the PRV. This results in controlled emissions reduction whilst reducing the baseload on the effluent handling system as the ongoing handling of the “standard” emissions will be dramatically reduced.
The combination of pressure relief valves and upstream rupture discs will largely eliminate the ongoing emissions under normal operating conditions whilst the safety of the installation against overpressure conditions remains at the required level. Baseload of the emergency handling system is reduced, resulting in most effective investment usage whilst emission fines are avoided.
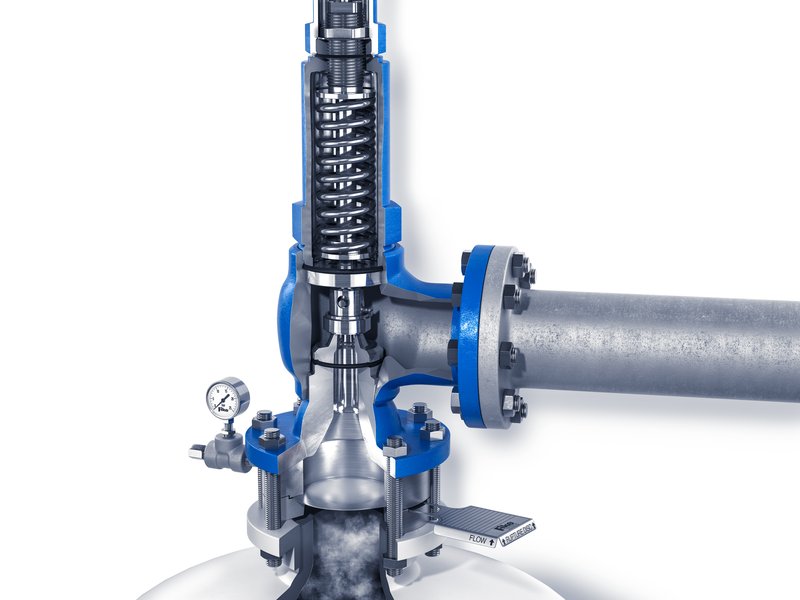
“The combination of pressure relief valves and upstream rupture discs will largely eliminate the ongoing emissions under normal operating conditions whilst the safety of the installation against overpressure conditions remains at the required level.”
Roger Bours