Hydrogen embrittlement causes metals to become brittle as a result of the introduction and diffusion of hydrogen into a material. This phenomenon causes reduced ductility and a lessening of load-bearing capacity below the anticipated proof or yield strength of the susceptible materials.
Cracking may then occur when sufficient stress is applied to a hydrogen-embrittled object. Such stress states can be caused both by the presence of residual stresses, associated fabrication operations such as forming and welding and applied service stresses.
These conditions can lead to severe damage and eventually failures of critical process components, and therefore hydrogen embrittlement must be avoided by adopting several of the following practices.
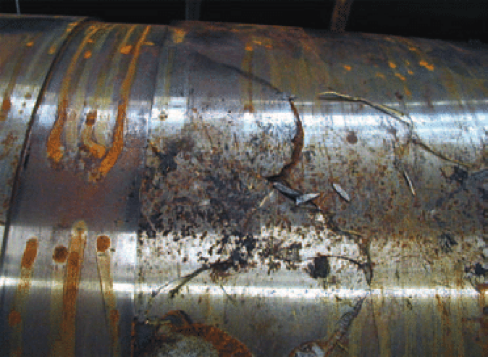
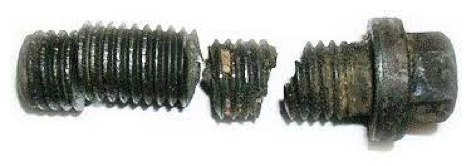
How Does Hydrogen Embrittlement Occur?
The degree of embrittlement is influenced both by the amount of hydrogen absorbed and the microstructure of the material. For example, microstructures with high strength or hardness levels, or having specific distributions of grain boundary particles or inclusions, can result in increased susceptibility to embrittlement.
Hydrogen is normally only able to enter metals in the form of atoms or hydrogen ions. Gaseous hydrogen is not absorbed by metals at temperatures ranging from ambient to approximately 150°C, as it is in molecular form, in which pairs of atoms are tightly bound together. However, as the temperature rises, the molecules tend to dissociate into individual atoms allowing absorption at temperatures which, for example, are associated with petroleum refining or heat treatment procedures. Higher rates of absorption are experienced in molten material, meaning that casting and welding operations can provide particular opportunities for the entry of hydrogen into metallic materials. Hydrogen ions are also produced by reactions associated with processes such as corrosion, electroplating and cathodic protection.
Cracking associated with hydrogen embrittlement has been given a variety of names depending on the situations in which it occurs. Commonly used terms include:
- Cold Cracking and Delayed Cracking
-
Often associated with hydrogen cracks that can form during cooling of the weld metal and workpieces after welding of steels.
- Hydrogen-induced Cracking (HIC) or Hydrogen Pressure-induced Cracking (HPIC)
-
A specific morphology of cracking occurring in steel pipelines and vessels which absorb hydrogen during service.
- Hydrogen-induced Stress Cracking (HISC)
-
Cracking experienced in duplex stainless steels.
- Environmentally-assisted Cracking (EAC)
-
Occurs due to interaction between the component and the surrounding service environment; hydrogen is only one of the agents which can be responsible for this type of cracking.
- Disbonding
-
Relates to the spalling of internal, weld-deposited cladding in vessels used for processing with high temperature hydrogenous gases.
- Stress Corrosion Cracking (SCC)
-
Some specific mechanisms of this phenomenon are related to interaction with hydrogen.
- Sulphide Stress Cracking (SSC)
-
Corrosion in environments containing hydrogen sulphide can cause hydrogen absorption and cracking.
How Can Hydrogen Embrittlement be Prevented?
This phenomenon can be prevented by minimising the contact between the metal and any sources of atomic hydrogen. In potentially corrosive service, environmental conditions should be controlled so that hydrogen ions are not generated by reactions on the metal surfaces. It is also seen that surface imperfections, when exposed to free hydrogen ions, tend to facilitate the occurrence of hydrogen embrittlement. In practical terms, this means that the metal should be of smooth surface and without cavities or surface imperfections.
If significant levels of hydrogen are likely to be absorbed during the processing operations, embrittlement problems can be avoided by using thermal exposures sometimes known as “baking procedures,” which allows hydrogen to escape before exposure to critically low temperatures. In some types of equipment, shutdown procedures are employed in which cooling rates are controlled to enable hydrogen levels to reach suitably low values before low temperatures are reached.
Another method for preventing the problem of embrittlement is through material selection, such as using materials that are less susceptible to hydrogen embrittlement:
- Stainless Steels (such as 304 & 316) - Generally more resistant to hydrogen embrittlement compared to other types of stainless steels.
- Duplex Stainless Steels - Combining the benefits of austenitic and ferritic stainless steels exhibits good resistance to hydrogen embrittlement.
- Nickel Alloys (Inconel and Monel) - Known for their resistance to hydrogen embrittlement and commonly used in high-temperature and corrosive environments.
- Titanium Alloys - Suitable for applications in aerospace and chemical processing.
- Aluminum Alloys - Specifically those in the 2000 and 7000 series are known for their resistance to hydrogen embrittlement.
- High-Strength Low-Alloy (HSLA) Steels - Some low-alloy steels with specific compositions and heat treatments may exhibit resistance to hydrogen embrittlement.
- Martensitic Stainless Steels - Certain martensitic stainless steels may be resistant to hydrogen embrittlement under specific conditions, but their susceptibility can vary.
- Precipitation-Hardening Stainless Steels - Certain precipitation-hardening stainless steels, like 17-7 PH, may exhibit resistance to hydrogen embrittlement.
It's important to note that the resistance of materials to hydrogen embrittlement can depend on factors such as temperature, pressure and the specific hydrogen environment. Additionally, proper material selection alone may not be sufficient; other measures such as design considerations, control of hydrogen concentrations and appropriate heat treatments may also be necessary to mitigate the risk of hydrogen embrittlement.
When dealing with critical applications or industries with high hydrogen exposure, consulting with materials engineers and subject matter experts is essential to ensure that the selected materials meet the specific requirements and standards of the given application.
ISO (International Organization for Standardization) has several standards that address various aspects of materials, including those related to hydrogen embrittlement. It's important to note that standards are periodically updated, and new standards may have been published since then.
Here are a few ISO standards that are relevant to materials and hydrogen embrittlement:
- ISO 15156: "Petroleum and Natural Gas Industries - Materials for Use in H2S-Containing Environments in Oil and Gas Production" - Provides requirements and recommendations for the selection and qualification of metallic materials for use in equipment exposed to hydrogen sulphide (H2S) in oil and gas production environments. Hydrogen embrittlement is one of the concerns addressed in this standard.
- ISO 11114-4: "Transportable Gas Cylinders - Compatibility of Cylinder and Valve Materials with Gas Contents - Part 4: Test Methods for Selecting Steels Resistant to Hydrogen Embrittlement” - Specifies test methods for selecting steels that are resistant to hydrogen embrittlement for use in gas cylinders.
- ISO 18086: "Hydrogen Embrittlement of Steels - Determination of Threshold Stress Intensity Factor for Hydrogen-Assisted Cracking” - Provides a method for determining the threshold stress intensity factor for hydrogen-assisted cracking of steels.
- ISO 20123: "Hydrogen Embrittlement of Steels - Determination of Threshold for Rapid Cracking under Sour Service Conditions" - Specifies a test method for determining the threshold for rapid cracking of steels under sour service conditions, including the effects of hydrogen embrittlement.
Rupture Discs and Hydrogen Embrittlement
Most materials as used for rupture disc seals are acceptable for use in pure hydrogen media. Hydrogen embrittlement is generally not an issue when dealing with rupture discs; however, the use of ferritic materials such as carbon steels for rupture disc holders is not recommended.
If you have questions about ensuring your pressure relief devices are immune to hydrogen embrittlement or if you require an expert to perform an analysis of your process, don’t hesitate to contact a Fike consultant: