Premium Pressure Relief
Fike's proprietary G2 manufacturing technology results in reverse-acting rupture discs with the best operating ratios, burst tolerances and cycle life available.
Fike's Patented G2 Manufacturing
What Does G2 Mean for You?
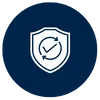
Superior Reliability
Features our highest operating ratio of 95 percent, allowing production facilities to run at full capacity without worry of altering burst pressure.
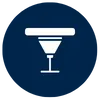
Extraction Scoring
Opening feature is laser-ablated or milled, not scored, providing an ultra-reliable line of weakness not found in work-hardened scoring methods.
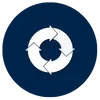
High Life Cycle
Superior cycling performance for processes running from full vacuum to 95 percent of burst pressure. Extremely high cycle life profiles available for less demanding cyclic conditions.
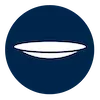
Backpressure/Vacuum Resistant
Concave surface faces the process side and can withstand full vacuum without added support; also ideal for in situ testing of pressure relief valves.
G2 Product Family
Examining Opening Features
Premium Pressure Relief Thought Leadership
Minimizing Hydrogen Leakage from PRVs with Upstream Rupture Discs
Hydrogen processes often use pressure relief valves (PRVs) to protect against overpressure events, but these devices are susceptible to leaking valuable and flammable hydrogen emissions. Learn how rupture discs may be used in tandem with PRVs to minimize leaking and improve cost of ownership.
How to Prevent Embrittlement
Embrittlement is a loss of metal ductility caused by exposure to hydrogen that can lead to severe damage and failures of critical process components. Because rupture discs are considered critical process component, learn how Fike safeguards rupture discs from embrittlement.
Preventing Contamination with Rupture Discs
Combating product contamination is critical because of the effect an impure batch can have on the business and most importantly to its users.
Hydrogen Embrittlement
Hydrogen embrittlement causes metals to become brittle as a result of the introduction and diffusion of hydrogen into a material. This phenomenon causes reduced ductility and a lessening of load-bearing capacity below the anticipated proof or yield strength of the susceptible materials.